Robots can work tirelessly in adverse conditions. Robotics and simulation are key elements in advanced manufacturing. Hazardous tasks can be simulated before actual implementation, thus avoiding injuries and loss of human life. Well-designed simulations for robotic applications are today being deployed for industrial and scientific use in real world scenarios such as the study of volcanoes, in space centres, for underwater exploration, in military operations, and so on.
Robotic platforms provide the software, databases and conventions that can be used to meet the challenge of developing complex robot actions across a wide range of real-time industrial situations.
Scientists can use a number of free and open source robotic platforms and simulation libraries to automate their work and predict results. Once the results on simulations and robotic platforms are found suitable, further actions can be planned.
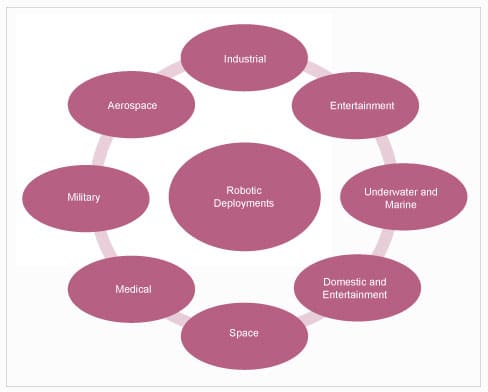
Challenges that appear simple to humans differ hugely between instances of robotic activities and conditions. Such robotic systems help a lot in the sensitive environments where automated machines or programmable devices are placed. Scientists and data analysts can fetch the data via satellite or assorted wireless protocols from a remote control room.
The typical features of robotic platforms include:
- Importing templates from CAD for mechanical and production engineers
- Integration of OpenStreetMap and Google Maps for real-time locations
Easy interface to work - Plugins and icons for different automations including automobiles, space, drones, aerospace vehicles, volcanoes, oceans, aircraft and many others
- Integration with multiple programming languages for customisation of features
- Exporting the results in multiple formats
- Association with multiple libraries of different engineering domains for compatibility
Table 1 lists the free and open source robotics development frameworks that are being widely used for industrial, social, corporate, military and related applications. These are programmable libraries that can be customised as per the requirements of the domain in which they are implemented.
Robotic simulation platform | URL |
Webots | cyberbotics.com |
Gazebo | gazebosim.org |
Robot Operating System | ros.org |
Open Robot Control Software | orocos.org |
Yet Another Robot Platform | yarp.it/git-master |
Mobile Robot Programming Toolkit | mrpt.org |
Robotarium | robotarium.gatech.edu |
Poppy-Project | poppy-project.org |
CoppeliaSim | coppeliarobotics.com |
Using CoppeliaSim for industrial and corporate applications
CoppeliaSim is a cross-platform tool for simulation and industrial robotic applications. This tool makes it possible to create portable, scalable and easy-to-maintain simulations for multiple scenarios.
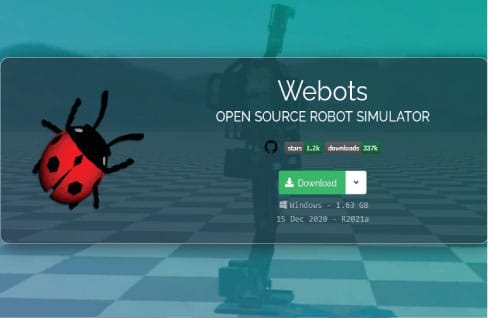
This framework has interfaces to various programming languages like C, Lua, Java, Python, Matlab and Octave. For an interactive production environment, the CoppeliaSim Robot Simulator relies on a distributed control architectural system in which the individual control of each object or model requires an embedded script for high performance applications. Such features give CoppeliaSim extremely versatile and adaptable powers for a broad range of robotic systems.
CoppeliaSim is used in the development of high-speed algorithms, as well as for plant modelling, rapid prototyping, validations, automated double-checking, etc. This feature-rich tool performs very effectively for a range of applications in domains that include engineering, military, aerospace, and health sciences.
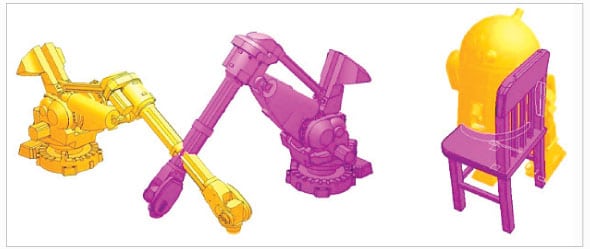
This tool converges dynamics and physics, and uses bullet mechanics, differential equations and other integrations for easy and effective calculations that simulate real life scenarios including collision reaction, grabbing, collision response, and grasping. Multiple recordable data sources (including user-dependent) can view or combine time graphs with xy-graphs. 3D curves can also be achieved effectively. CoppeliaSim integrates features for real-time automations including proximity sensors, vision sensors, and viewable objects.
Collision detection and avoidance in CoppeliaSim
If a robot is developed for industrial and corporate applications, it should be programmed in such a way that it does not collide with other components or machinery in the industrial unit.
The collision detection and avoidance module is easy to program in CoppeliaSim. The distance and collision settings can be set up effectively in Menu->Tools->Calculation.
Researchers and scientists can carry out research tasks using open source platforms and tools like CoppeliaSim for robotic applications, whenever the real world infrastructure and devices are too costly to work with.